The Importance of Fabrication in Construction: How it Shapes AEC Industry
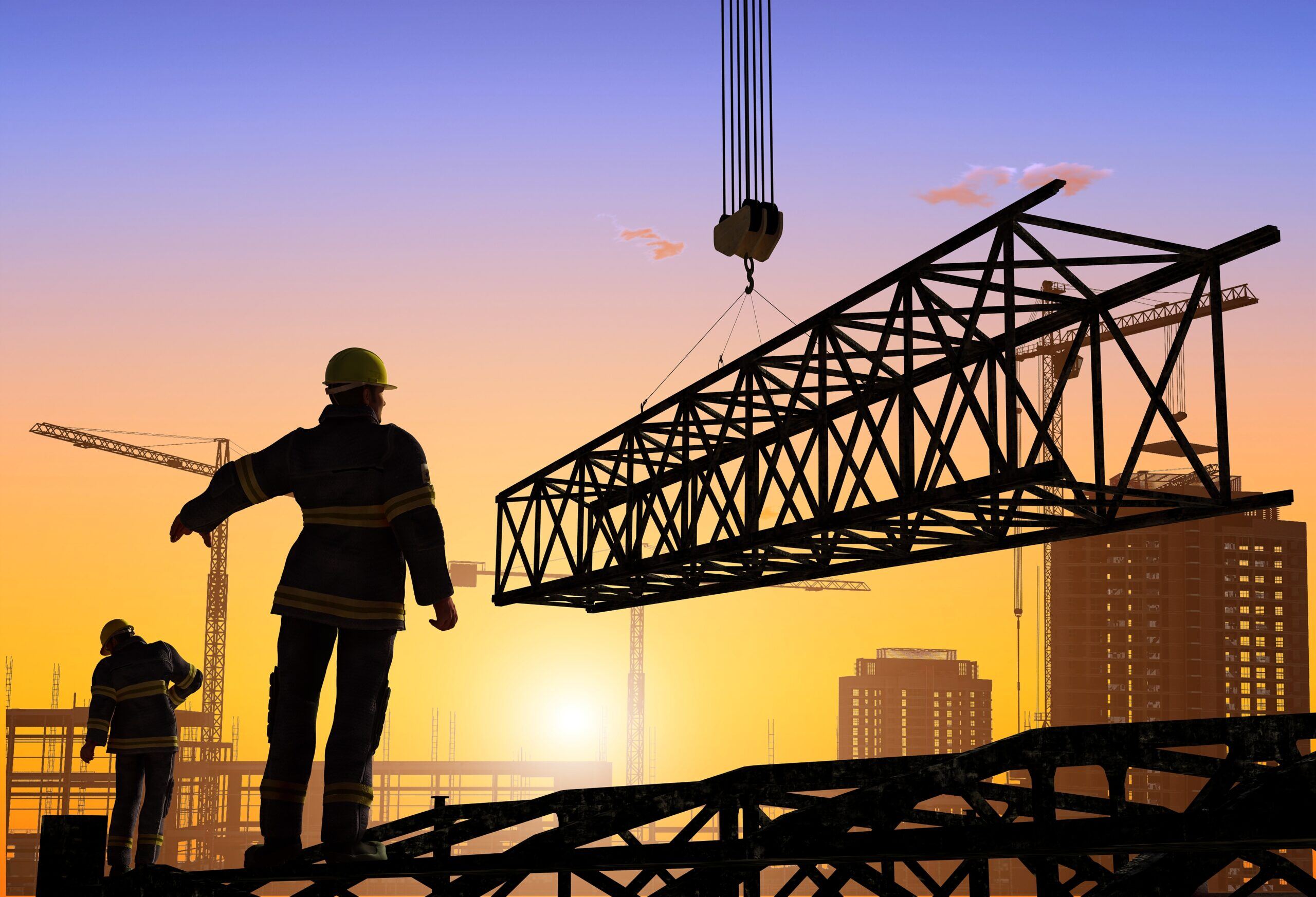
Table of Contents
Fabrication in construction, along with software technology, has created wonders that were never thought possible before. New opportunities at an unprecedented rate have encouraged designers to further research fabrication projects and methods. In this blog, we present to you the significance of fabrication in construction through four major benefits.
What is Fabrication in Construction?
Fabrication is the process of constructing or manufacturing something through machines that are automated by computers. The term ‘digital fabrication’ has been gaining interest in the past decade as a means to enhance manufacturing through the use of digital software technology. Far from being a new term, it is the innovation behind the works of Frank Gehry’s works in the early 90s, namely the Barcelona Pavilion and Guggenheim Bilbao.
Now, digital fabrication is not only in use for manufacturing but also in construction itself to prefabricate parts of a building or 3D print a whole structure.
While it has taken time for the industry to adopt digital technology such as BIM (Building Information Modelling).
The AEC industry has taken up fabrication rather well and quickly. After all, it was easy to see how time-saving fabrication techniques can be. Moreover, the learning curve to use this technology is less steep than BIM (unless we are talking about complex production), which is why we still see many architects hesitant to adopt BIM.
How Is it Used in the AEC Industry?
Architects, designers and engineers have relied on fabrication to speed up construction as an efficient production process. We know that the AEC industry operates on a project-based approach – each project is unique, and challenges and solutions for each project will also be dissimilar. Such an approach requires efficiency in both resources and time, which traditional construction methods lack.
Fabrication in construction, with digital technology, has provided speed and accuracy. The list of digital fabrication technologies is also getting longer, from different types of 3D printing to CNC machining and robotics. Through intelligent 3D models, we can now fabricate parts of a building and assemble them on-site. We call this process ‘prefabrication’. Now, technology has taken it a step further to produce, or more precisely 3D print, a whole building structure.
Fabrication methods like 3D printing go hand in hand with generative design methodology. Learn what this advanced design process is all about here - Generative Design in Architecture Explained.
Importance of Fabrication in Construction Industry
Why do we need fabrication in construction? For a simple, but greatly significant, reason – high efficiency, accuracy and quality output. Fabrication has skyrocketed the productivity rate of manufacturing and construction by overcoming the old barriers that hindered production.
Output
Fabrication processes are not as simple as creating CAD drawings and sending them to the machine. Perhaps the main reason for their popularity is that digital fabrication allows for the creation of the most complex forms or products. It does so by using other tools and digital technologies like BIM and computational modelling. Create the entire design in a BIM software like Autodesk Revit, ready the file to be fabricated, either 3D printing or CNC machining, be patient and voila! The pre-fabricated item is ready to be shipped to the site for assembly.
Not only does it take less manpower, but also causes less pollution on site. This is why prefabrication is also considered an ecologically sound process. Conventional on-site construction requires large quantities of materials to and fro the site, not to mention the subsequent waste, which naturally builds up the carbon footprint. Prefabrication cuts down on the carbon footprint by a good margin, a fact that contributes to its quick uptake in the industry.
Efficiency
The efficiency of digital fabrication in construction and manufacturing is evident in 4 areas:
- Time
- Material resources
- Cost
- Manpower
The fabrication equipment is controlled by computers with minimal human input. Yet, they are faster and more accurate than the average human output.
Each pointer and nozzle in a machine moves according to its programme and the imported CAD file. Within a few minutes, we can easily laser-cut multiple panels or even curved shapes. Depending on the type of 3D printing and fabrication materials used, we can conveniently produce limitless designs without the designer getting involved in the process. That means while we wait for the one product to be 3D printed, we can start designing the next one right away.
The accuracy it provides also directly affects the materials saved. Miscalculated measurements are one of the issues of human error in construction and production. Fewer human errors means less material wasted. The need for fewer materials will also reduce the overall cost incurred so fabrication methods can be both economical and sustainable in the long run.
Find out what it means to be sustainable in architecture with our ultimate guide to sustainable architecture.
Here is a point of contradiction – some might argue that certain fabrication methods like 3D printing are costly. That is also true. It largely depends on the type of fabrication materials used, the amount and the size of the product. Nonetheless, we can expect this to change in the near future as more advanced materials for 3D printing become more readily available.
Accuracy
How good is speed if it’s fabricating inaccurate products? Luckily, we can easily note the positive change in both the speed and accuracy of the output.
The output from a fabrication process is almost completely accurate(that is, if you get the CAD drawing right) with even small details clearly visible. There is little human input once the CAD drawings have been transferred. The software and the machines handle the remaining process. The result is a highly accurate product with very few human errors.
However, it is also important to mention here that the accuracy level will also depend on how advanced the equipment is.
High Potential
The potential of fabrication in construction alone is limitless. It started off with designers creating prototypes to test a mechanical instrument or a building component. And it is still in use as a quick prototyping process. Fabrication equipment has become a lot more easily available, anyone can buy one for a few hundred dollars. This type of equipment does not have the high accuracy that more complex and expensive fabrication equipment boasts, but it is good enough for prototyping.
Additive manufacturing, or 3D printing, is usually the common process for prototyping. We can also laser-cut parts of a piece of furniture and assemble them. This subtractive manufacturing process requires larger equipment compared to additive manufacturing.
Prefabrication is now in use not only in the construction industry but also in automobile and other manufacturing industries. In recent years, we have seen architects and engineers experimenting with digital fabrication in construction to create both aesthetic and functional building elements. All the experimentation and exploration of technology has resulted in a new breakthrough – 3D printing of entire buildings. The 3D printing of a building is still rather slow and limits the size of the structure; but as technology continues to develop, we will see these challenges solved and the use of digital fabrication in construction soar.
Architects and engineers of today can consider themselves lucky – we are observing a digital revolution in the industry. The emergence of technological breakthroughs such as BIM, computational design, robotics and material science has multiplied the potential of manufacturing and off-site construction. They may seem like small feats, but the overall benefits these technologies have to offer are enormous.
To keep up with more insights from the AEC industry, head to our Resources section. We serve daily articles in emerging trends, technologies and career insights for young AEC professionals.