The Opportunity Cost of Not Adopting BIM in 2025
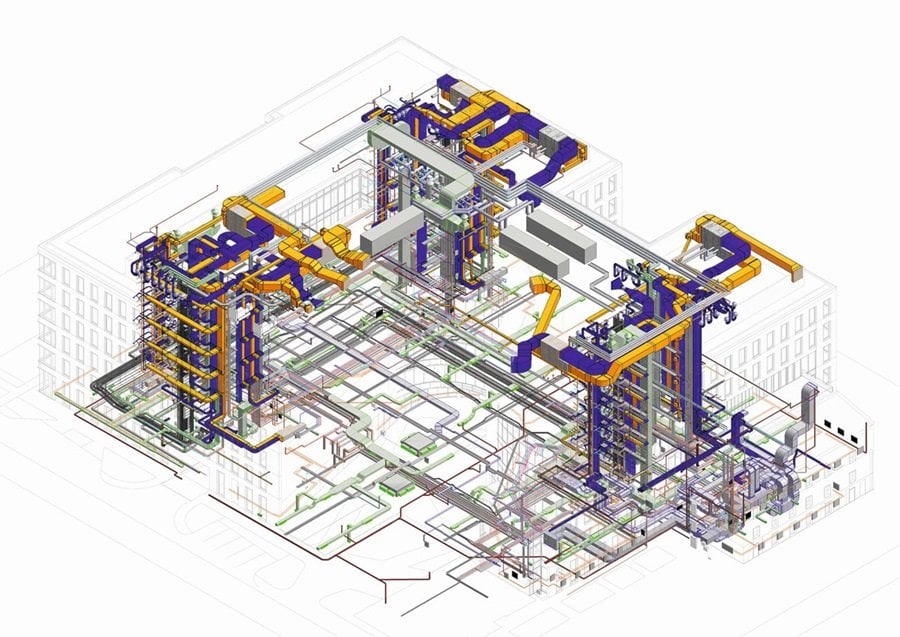
Table of Contents
What is BIM?
BIM, or Building Information Modeling, is a highly collaborative process that allows all the stakeholders involved in a project to plan, design, and construct a structure or building within a single 3D model. Many agree that BIM is the foundation of digital transformation in the AEC industry.
The key word in BIM is "information." BIM is centered on models made up of objects. The data in the model defines the design elements and establishes behavior and relationships among model components.
There are many benefits to using BIM, including increased productivity and collaboration, reduced construction costs and error risk, and a faster project completion time. Owing to these massive benefits, the industry is now adopting this new technology at breakneck speed. The following table lists the opportunities and obstacles surrounding the adoption of BIM in the AEC industry:
Adoption of BIM |
|
Opportunities | Obstacles |
Enhanced Collaboration, Coordination, and Communication | Investment required for robust hardware and software |
Supports pioneering/ Advanced techniques | Reluctance to adopt changing technologies |
Reduced Construction Cost | Lack of Government Mandates in developing nations |
Increased accuracy | Resources needed for training |
Decreased project handover time | Lack of awareness regarding BIM technology |
What is "Opportunity Cost"?
According to the Economic Times, the opportunity cost is the loss of potential benefits when an individual, business, or investor chooses one substitute over another. This opportunity cost can often be hidden, and the costs could go unnoticed very easily.
Therefore, it becomes important for a business to thoroughly understand this opportunity cost when choosing one investment over another. In the present scenario, many AEC firms are reluctant to adopt BIM, favouring traditional tools like AutoCAD instead. Let us look at the opportunity cost of not adopting BIM.
The Opportunity Cost of Not Adopting BIM
1. Lag in Industry Advancement
BIM is contributing to the advancement of the AEC industry with every passing year. Not only has the adoption of BIM brought an organized approach to technology integration in the industry, but it has also improved the collaborative process between various stakeholders.
From its inception, BIM has focused on advancing and aiding projects with interesting and inventive concepts like virtual and augmented realities, prefabrication, drones, the Internet of Things, and 3D printing, to name a few. All these incorporations have straightened out work processes and increased efficiency, which would have otherwise increased costs and overall delivery time.
Let us discuss these advancements in detail:
1. Prefabrication: Prefabrication refers to manufacturing construction elements off-site and later assembling them on-site. BIM enables prefab or modular construction with more efficient workflows than in traditional construction. This is because it enables digital design-to-fabrication workflows for all building disciplines.
2. Internet of Things: IoT, or the Internet of Things, describes the network of physical objects—“things”—that are embedded with sensors, software, and other technologies for the purpose of connecting and exchanging data with other devices and systems over the internet. Integrating BIM models with IoT nodes provides advantages including greater efficiency, ubiquitous real-time monitoring, and resource management.
3. Drones: Drones are increasingly being used by project managers and AEC professionals to record and report the progress of project construction. Drones can capture accurate project data over a large area in a short span of time. BIM specialists then use this data to refine their model and make the BIM modelling process more reliable for the project.
4. 3D printing: 3D printing or additive manufacturing is a process of making three dimensional solid objects from a digital file. BIM makes 3D printing more accessible for AEC professionals.
Read more: 6 Ways BIM Is Proving To Be The Future Of Architecture
2. Higher Construction Costs
Factors such as modern designs, specialized equipment and techniques required to work with materials, well-trained professionals, and workers - all add up to the overall construction cost.
Here’s how not adopting BIM can lead to higher construction costs:
1. Reduced Collaboration: Before the inception of BIM, all communication had to be done in person or through phone calls and emails. This would lead to project delays and an increased risk of miscommunication and factual errors. BIM helps teams collaborate on a single 3D model. Thanks to this, mistakes in the final version of the design are far less likely.
2.Miscalculations and bad budgeting decisions: Before the inception of BIM, cost estimates were calculated manually - which led to miscalculations and bad budgeting decisions. Thanks to BIM, architects can now allow the computer to assist with larger budgets. Once the program calculates a cost estimate, architects can deliberate on bringing down expenses by evaluating material use, selection of materials etc.
3. Great deal of time spent on deciding the right material: Before BIM, finding the right material as per the project’s and client’s requirements would be a time-consuming process. It would take days of scrolling through catalogues and negotiating with various vendors selecting the right fit, etc. BIM helps streamline this process by calculating how much a certain material costs, comparing different vendors, and giving the best fit for a project. And that’s not all! The software also alerts designers to particularly low market prices, suggesting a good time to make the purchase.
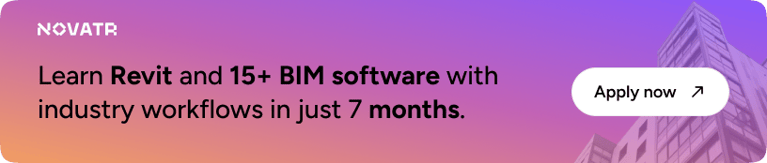
3. Reduced Efficiency
Let us first explore the reasons for reduced efficiency when using traditional tools. These include accommodating last minute changes by the client effectively into the design and calculating overlap between different stakeholders. Using BIM brings more clarity and a seamless working flow.
Here’s how not adopting BIM can lead to reduced efficiency:
1. On-site conflicts: BIM allows construction teams to resolve constructability issues early in the design process to prevent conflicts on-site. Through the integration of architectural, structural, and MEP facilities on a single 3D model, stakeholders are able to collaborate successfully and identify clashes through an automated process. Navisworks is a powerful software that can help teams achieve this.
2. Reduced time management: Time management is the process of organising a time strategy for work activities on a project. Before BIM, it was difficult for construction professionals to plan for the project, especially for back-ups in case of unfit site conditions, risks, or threats. 4D BIM allows convenient scheduling across design and construction stages, major or minor, and helps visualise the project development sequentially.
3. Reduced cost management: Before BIM, it was difficult for all stakeholders involved in a project to have accurate and transparent budget information to advance the work. BIM can be used for model-based cost estimation or 5D BIM. This allows all the relevant professionals to envision the cost of the ongoing and future activities to give estimates for the overall project expenditure.
Interested in knowing more about BIM dimensions? Check out: Dimensions in BIM: 7 BIM Dimensions Explained
4. Limited ability to compete
The AEC industry is an extremely dynamic and competitive one. As the industry undergoes rapid digitalization, it will be necessary for all firms to keep up with the advancing pace to stay relevant.
The following assessment helps analyze how not adopting BIM reduces an AEC firm’s ability to compete:
1. Lower ROI: Unlike with traditional tools, using a BIM system can help AEC firms effectively use their facility and asset documentation to tackle concerns like reactive maintenance practices, incomplete asset information, and employee inefficiency. This can increase ROI - and ultimately the business revenue.
2. Reduced Creativity: Traditional tools like AutoCAD don’t allow room for creativity for the designers to optimise their project workflows. This is unlike BIM software like Revit. Revit software API can be used to enhance creative problem solving in a design process. Custom Revit API tools are often created to help with productivity and or build professional add-ins.
5. Increased risk of error
Finally, BIM helps project teams make fewer errors by identifying clashes at an early stage. This helps reduce the project's time and cost.
Let’s see how not using BIM increases the number of errors:
1. Excessive clashes: As mentioned earlier, BIM aids in speeding up the traditional project construction by identifying clashes between multi-trade models during the early design stage. Autodesk’s Navisworks is a BIM clash detection platform that identifies and resolves the hard clashes based on the geometric and rule-based algorithms embedded in the building design components.
2. Decreased Transparency: Without using BIM, there is no way to understand the stage at which an intentional design error occurred. BIM allows for greater transparency during the development stages, thus effectively reducing the likelihood of false progress reports and project estimation manipulations occurring.
3. Decreased Coordination: In traditional construction projects, communication is often difficult, with each stakeholder working in isolation. Thanks to BIM, all collaborators can work on a single 3D model, enabling real-time collaboration.
In Conclusion
BIM is a powerful tool that helps construction teams reduce the risk of errors, helps them stay competitive, increases project efficiency, helps reduce construction costs, and also helps with the advancement of the industry as a whole. This is the right time to dive deep into enhancing and building on your skills if the thought of learning BIM has been lingering in your mind.
Want to get started learning BIM and availing its advantages?
Novatr offers a course on one of the most in-demand skills in the present AEC industry—the BIM Professional Course. Mentored by leading industry experts with established real-world experience, you will also be exposed to real-life projects, giving you a chance to practice as you learn.
Head over to our Resources page to get more insights on AEC careers, software and tools, and industry trends.